Warranty Maturity Model:As a proof of concept, IDC and the iWCM are asking all warranty professionals to take a brief survey to help verify that their responses can be used to assign a relative level of maturity to their warranty processes.
The warranty industry is about to get its very own maturity model, if enough warranty professionals help to test the model and validate the theories behind it by taking a brief survey that's going online today.
The maturity model is designed to apply across industries to the warranty processes underlying everything from air conditioners to airplanes. Team members who helped put the maturity model together have diverse backgrounds in the automotive, high tech and white goods industries. And to help make the results applicable across all industries, they decided to minimize the requests for raw numbers and measurements, and to instead ask about what tools are in use or whether warranty coverage might vary by product, by customer, by country, or by some other metric.
It was inspired by some comments made by Joe Barkai, practice director for IDC Manufacturing Insights' Product Lifecycle Strategies research service, during a panel discussion he hosted at the Warranty Chain Management Conference in Los Angeles on March 3. Barkai was one of six people who were part of the "Design for Warranty and Customer Self-Repair" track.
Warranty Week covered that presentation in a "Design for Warranty" article published on March 11, 2010. In that newsletter, we briefly noted that Barkai displayed a maturity model in which companies begin to support customer self-repair at a basic level, and then move on to more advanced levels. The next-to-last slide in Barkai's presentation is the one we're reproducing below:
Figure 1
Design for Self-Repair
Maturity Model
Source: IDC Manufacturing Insights
Barkai said the lowest stage in this Design for Self-Repair maturity model would be one where customer self-repair is unsupported. Anyone who tries to fix their own unit will void its warranty. The highest stage would be one where the manufacturer is proactively monitoring the product, diagnosing problems before they become failures, and shipping parts or arranging for repairs before they're even requested.
In other words, by observing several behaviors and policies, one could make some observations about the relative maturity of a company's design for self-repair effort. And then if anyone asked about the wisdom of moving up the chart to a higher stage, one could provide them with data about the costs and benefits of a trained help desk or an analytics software package, for instance.
Now, the idea of defining a maturity model has broadened to encompass not only customer self-repair, but also every other facet of the warranty process. And it's involving not only Joe Barkai and IDC Manufacturing Insights but also the Institute for Warranty Chain Management.
Cost-Benefit Analysis
Barkai said it's not the first time IDC Manufacturing Insights has helped to define a maturity model. He said they are used in several areas within the supply chain and product lifecycle practices. End users increasingly want to know the business value of a new project or a new policy before implementing it. And maturity models help them understand where they are in relation to their peers, versus where they could be.
"We're finding that the concept of a maturity model is very important," Barkai said, "because very often we deal with improvement, whether it's new software or a process improvement. And the question always is, why should I do that?"
The days when features and functions helped software to sell itself are long gone, Barkai said, although the sale of warranty software has never been particularly easy. "We really need to understand why we are doing certain things, and therefore what are the associated metrics, so we can understand what we need to improve and we can measure improvement. So we find that a maturity model as a concept is a very convenient framework for decision-makers to understand the need, to define it, and to explain the business value to executives," he said.
And so, what began as an example of a maturity model specific to design for customer self-repair turned into an effort to define a maturity model for warranty in general. In such a model, the lowest maturity level would be one where transactions are processed and claims are paid, but little else is done with the data. The highest level might be one where warranty data also has a quality function: It is thoroughly analyzed and is used both to improve current production and to influence future designs.
Looking for Maturity Markers
The theory is that the presence or absence of certain warranty-related technologies, people, processes, or activities can help define the relative maturity of a company's warranty operation. For instance, as in the above slide, the use of some kind of analytics software would generally be a marker for a company with a relatively mature warranty process. The availability of minimal documentation would be one of several markers for a very basic operation.
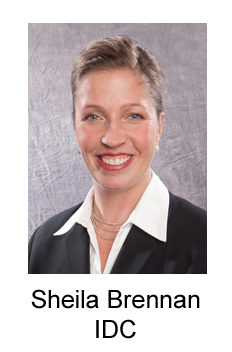 But how can we tell which company is at what level? The fastest route is to ask people some questions, and let their responses help us figure it out, according to Sheila Brennan, program manager of IDC Manufacturing Insights' Product Lifecycle Strategies practice.
Brennan joined IDC in June, after spending almost six years working at AMR Research. While there, she ran a manufacturing peer forum, where operations and IT executives came together to discuss manufacturing issues and to share best practices. Brennan would recruit the expert analysts and guest speakers who also participated, and would schedule the teleconferences and facilitate the agenda creation.
Brennan also has worked extensively on supply chain issues, working with companies on benchmarking everything from consumer products to industrial equipment. And she tracked the technologies they were using, and documented their best practices.
Turning Metrics Into Models
"We would collect over 75 metrics from each company," Brennan said, "and I would work on these engagements with them to understand not just what their metrics were, but to also understand their business goals and pressures. And we'd turn all that information and data around to tell them a story: Here's what we're seeing. Here's how different metrics impact each other and where their focus should be."
In other words, she has a long history with the task of turning survey responses and measurements into a comparative profile, and then telling that story to the client. "We would paint the whole picture, and we would help organizations understand in a way that they hadn't really looked at their business before," she added. "And we would be working with cross-functional teams that wouldn't normally come together."
Soon after Brennan joined IDC, Barkai told her about his hopes to develop a maturity model for warranty. Previously, she said, in most of the manufacturing and supply chain projects she'd been a part of, warranty was something of an afterthought. But here, warranty was the focus.
"I looked at that as a huge opportunity," Brennan said, because while it was still within her "comfort zone" of manufacturing and supply chain, it was something nobody had really done before. "This is my opportunity to leave my thumbprint on industry and also contribute in a much needed area," she said.
From her past experience, Brennan said she's ready to deal with the two major problems that always seem to pop up. First, employees are sometimes initially afraid that they'll give a "wrong" answer or a "bad" number that will somehow help end their employment. Brennan said they need to be reassured up front that they're looking to continuously improve the process, not replace it, so there's no fear of layoffs resulting from the survey responses.
Not Writing Shelfware
Brennan also said that the ability to accept the results and to act upon them is itself a sign of maturity. Otherwise, she said, the data becomes "shelfware," which will sit there until the next time someone tries to change the process. So executive "champions" need to be involved and help employees understand that there will be changes, and hopefully improvements.
Brennan said she hopes the survey takes 20 minutes or less for each participant to complete. The questions are designed to help provide a company with a realistic assessment in terms of where they are along the warranty maturity model. It's almost like a grade level reading score given in school -- "you are reading at the tenth grade level." So there are no "right" or "wrong" answers. And, in fact, because this hasn't been done before, there aren't even any averages or medians yet. And that's why we need warranty professionals to take the survey and help to test the model.
There have been some similar projects within specific industries, however. For instance, in 2008, the Automotive Industry Action Group and Original Equipment Suppliers Association collaborated to form the Consumer-Centric Warranty Management work group.
AIAG and OESA assembled volunteers from both OEMs and suppliers to study quality and warranty issues, and to determine if there were best practices the industry could adopt as a whole to further reduce warranty costs. Leading participants included representatives from Robert Bosch LLC and Metaldyne, as well as from Chrysler, Toyota, Delphi, Denso, Federal-Mogul, and Freudenberg-NOK, among others.
Warranty Management Guideline
The effort was focused on ways to reduce the cost and the quantity of recurring warranty issues in the automotive industry, such as incidents where no trouble is found. These types of incidents are especially frustrating to the consumer, who is likely to return with the same complaint a short time later. Extensive information on NTF reduction strategies and numerous case studies about the NTF problem were included in a guideline the groups published, which is now in its second edition. AIAG and OESA sell copies of the "Consumer-Centric Warranty Management Guideline" to their members for $49.
Brennan said she recently traveled to Detroit to take the AIAG's Consumer-Centric Warranty Management training course. And she spoke with members of both the AIAG and OESA. Brennan said she found the AIAG/OESA efforts to be quite complementary to the Warranty Management Maturity Model, with little overlap.
"They look at our model as a way to bring more attention to warranty management overall, especially at the executive level," Brennan said. "Which is their goal too." And once this first round of maturity model data collection is completed, Brennan said she intends to brief both the AIAG and OESA on the results.
The First Round
"What we're doing right now -- the first round of survey -- is initially just to vet the model," Brennan said, "to see if what we put together as our model: the phases, and the different dimensions of organization, process governance, measurement and technologies, are in the right place. And we want to see if the model reflects how practitioners across industries view their business."
To help ensure first pass success in the model's development, Brennan and Barkai enlisted several seasoned warranty practitioners from automotive, high tech and white goods industries to join the core model development team early this summer. But now they need additional testers to actually take the survey and help to prove that the responses actually correlate to a warranty maturity level.
Once the model is proven, Brennan said, she expects that companies will use the survey to assess themselves, and to see where they stand in relation to others. "It goes back to the old adage, 'If you cannot measure it, you cannot improve it,'" she said. [attributed to Lord Kelvin]
But more than just measuring where they are now, Brennan said she hopes that the survey and the discussion that surrounds it will also lead to an assessment of what else is out there in terms of best practices and technologies, what everyone else is doing, what's working, and how a given company can get itself and its warranty process to a higher level of maturity. The goal is not simply to reduce cost, but ultimately to raise profitability levels, by improving quality, boosting reputation, increasing customer satisfaction, and improving sales.
"We're hoping that folks can plot themselves in a way that they can decide where they think they're going to get the most bang for their buck in making investments going forward and refining their processes," Brennan said. Down the road, she added, the effort may actually help them make their technology choices, based on what they see is working for others.
Institute for Warranty Chain Management
Once finalized, IDC Manufacturing Insights intends to release ownership of the model to the Institute for Warranty Chain Management and its members for future maintenance, Brennan said. As with some other supply chain benchmarking projects she's been involved with, it's always best for a small group to get the project started and then to hand it over to much larger group for the long term.
"We want a non-profit, member-driven organization to continue to propagate the use and maintenance of this model," Brennan said. "We feel that it's in the best interest of everybody involved, and all the users of the model, to have it be a membership-driven maintenance process going forward." And the iWCM is the best candidate for that process to happen.
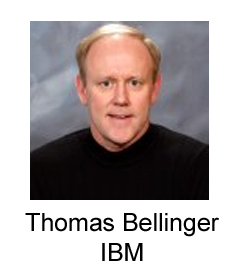 Thomas Bellinger, a founding member on the iWCM's Board of Directors and a global warranty management subject matter expert at IBM, said this is exactly the kind of activity that the institute needs in order to gain traction within the warranty profession. It fits right in with the iWCM's goals to provide education and certification services to the industry, he added.
"We believe that once businesses become aware of this maturity model, it will provide them with an assessment that hopefully they'll use to establish an improvement process," Bellinger said. Part of that improvement process will include education, and ultimately certification in warranty chain management, which the institute will provide, he said.
Early iWCM Involvement
The iWCM, Bellinger added, was involved in the development of the maturity model right from the start. Within hours of the "Design for Warranty and Customer Self-Repair" panel discussion on March 3, Barkai was discussing the possibilities of the maturity model with Glen Griffiths, the iWCM's president and the director of Hewlett Packard�s Global Engineering Services.
When Bellinger reached out on March 17th to IDC Manufacturing Insights with an invitation to collaborate on some of the institute's planned educational activities, Barkai suggested that the maturity model would be the perfect platform for IDC to become more deeply involved in those activities. That led to an internal iWCM board discussion, and then to a series of recruitment emails between iWCM members.
Bellinger emailed Warranty Week editor and iWCM member Eric Arnum on April 14, asking if he would be interested in participating in the development of the maturity model. Other iWCM members received similar messages, and an initial conference call to discuss the maturity model occurred on May 4. Eventually, the team expanded to include not only Bellinger, Barkai and Arnum, but also Brennan and Ben Friedman from IDC, John Shane from appliance maker Whirlpool Corp., Marc McKenzie from the consultancy Innovation Blue LLC, and Daryl Kreskowiak from the automotive industry.
Brennan was introduced to the team during a June 25 conference call, and then serious work began on the creation of a set of survey questions. There were two more conference calls in August and one marathon session in early September and as of last night, the survey is online and ready to be used at: http://web5.kinesissurvey.com/idcglobal2/html.pro?ID=134
Results in March 2011
Once the survey results have been collected, the task of analyzing the results will fall to Brennan and Barkai. Inevitably, there will be a few more conference calls this fall and winter, leading up to a general release of the results at the next Warranty Chain Management Conference in March 2011.
"We have secured a keynote slot," Brennan said, at the WCM Conference in San Diego. "Our keynote presentation will go over the entire framework of the model. And then we will have a much more detailed presentation in a 'theme track' for the day. We'll kick that off with a much more detailed presentation of the results from the study."
In that theme track, they'll make some comparisons between industries, if that turns out to be related to maturity. Or perhaps the results will vary by company size? Or maybe it will correlate to geography, or perhaps to the job title of the person in charge of warranty? We won't know until we have some data.
After the WCM Conference in San Diego, Brennan said IDC Manufacturing Insights plans to host a webcast for survey participants and their invited guests, to discuss the first round of results. And then it's onto the second round, and the refinement of the model, and then the handoff to the iWCM for future maintenance.
Bellinger said he hopes the model gets a pretty good shake-out in this first pass. "But I think the word maintenance is a key word in the referral to our institute," he noted, "because I think over time the markers will probably move. I'm hoping that the maturity level of warranty chain management can continue to expand, and that we can have much higher levels of maturity available to organizations. Therefore, we want to maintain it so that it can capture both those who are new to the subject and those who have fully embraced all that they can do from a warranty management perspective."
|